References
Our transporter can handle all types of solid materials and our customers come from a broad array of industries including metal, mining, automotive, automation, vision, furniture, recycle, food and pharmaceutical companies. For more references and details, do not hesitate to contact us.
Quick Stop and Back-Track Tray in favor of the vision system
August 2019, RVT Automation delivered a robot cell with 100 % functionality & satisfaction to a Swedish automotive company for feeding, mounting and quality assurance of steel clips. This robot cell handles 10 different products. Two linear conveyors present details to the vision system: correct-positioned details are picked up from the top tray and unpicked details are recycled via Back-Track Tray at a negative angle. The designer Markus Andersson compliments Conveyor 22’s unique technology:
– Good flow and distribution of details
– Good control: no loss of detail and no disorder unlike as in many other feeding systems
– The conveyors are equipped with Quick Stop to get as short a delay as possible between stop of conveyors and trigger of vision camera
– It is advantageous and affordable to recycle unpicked details to the buffer with Back-Track Tray in the same feeding system
Markus Andersson, Automation Engineer, RVT Automation AB, 2020-05-22
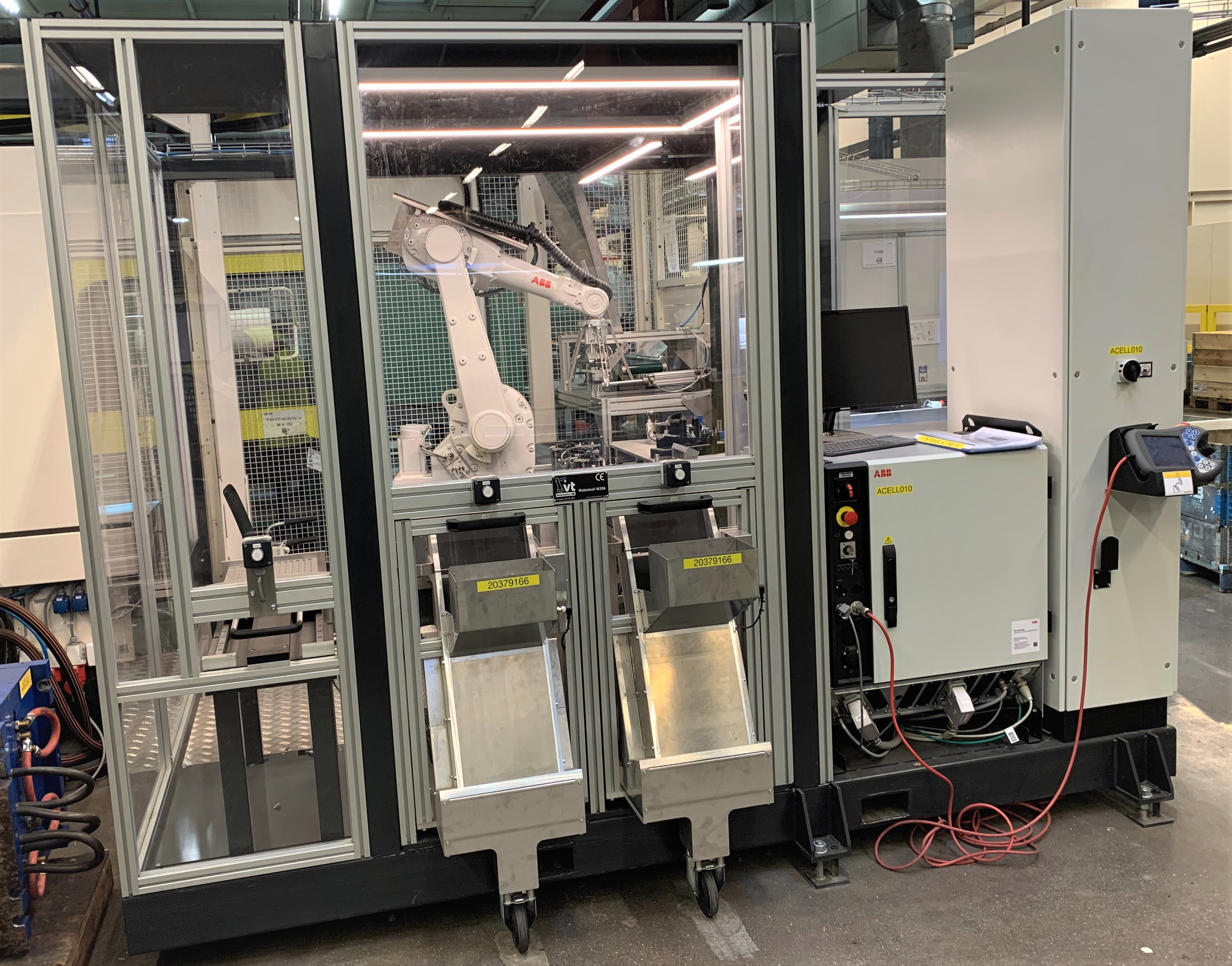
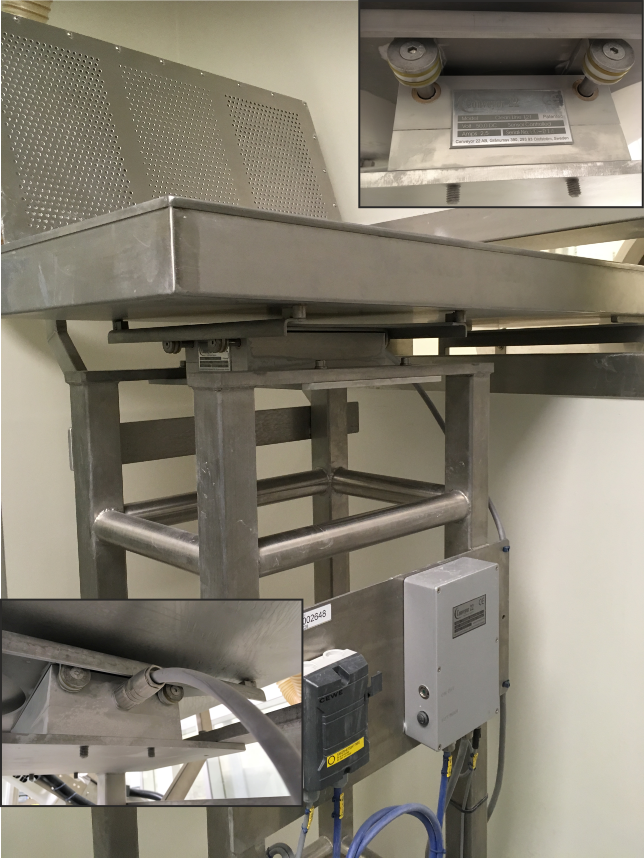
Clean Line 121 in Pharmaceutical Industry
April 2016, one Clean Line 121 was sold to a medical company in Sweden. Thereafter they have bought several more conveyors from us. Their demanding environment is dusty. Today we received feedback and pictures from their engineer.
– Appreciated quietness while operating.
– Constant flow without adjustments.
– Timely and effective technic supports.
We are super satisfied and plan to replace more vibration feeders by linear conveyors from Conveyor 22.
An anonymous customer, 2018-03-07
Compactness, digital control and built-in alarm made the choice for SCANIA!
In 2015, SCANIA in Oskarshamn bought the first conveyor. After 1.5 years of good experience, SCANIA decided to build 8 conveyors into its new stamping press tool. Production Technician Tobias Carreberg explains why:
– Firstly, we bought one for testing that worked well. We operated it manually.
– The main reason we chose Conveyor 22’s conveyors to build them into a big tool was that there was no space to fit in the height of belt conveyors. In the past, operating those belt conveyors also requested workload on just monitoring them.
– Another advantage is that Conveyor 22’s conveyors make our job easier. In case of interference, we get an alarm from the conveyor and we can see exactly where problems exist without troubleshooting needed. Thus, we do not risk getting scraps piled up which could cause tool damage.
– We are very satisfied with Conveyor 22.
Automation Technician Nicklas Nordlöf tells that:
– The electric conveyors are fully integrated into the stamping press tool and controlled by our PLC system. The evacuation duration of these conveyors is programmed from first punching to a few minutes after last punching.
Tobias Carreberg, Production Technician; Nicklas Nordlöf, Automation Technician, Scania CV AB, 2017-06-16

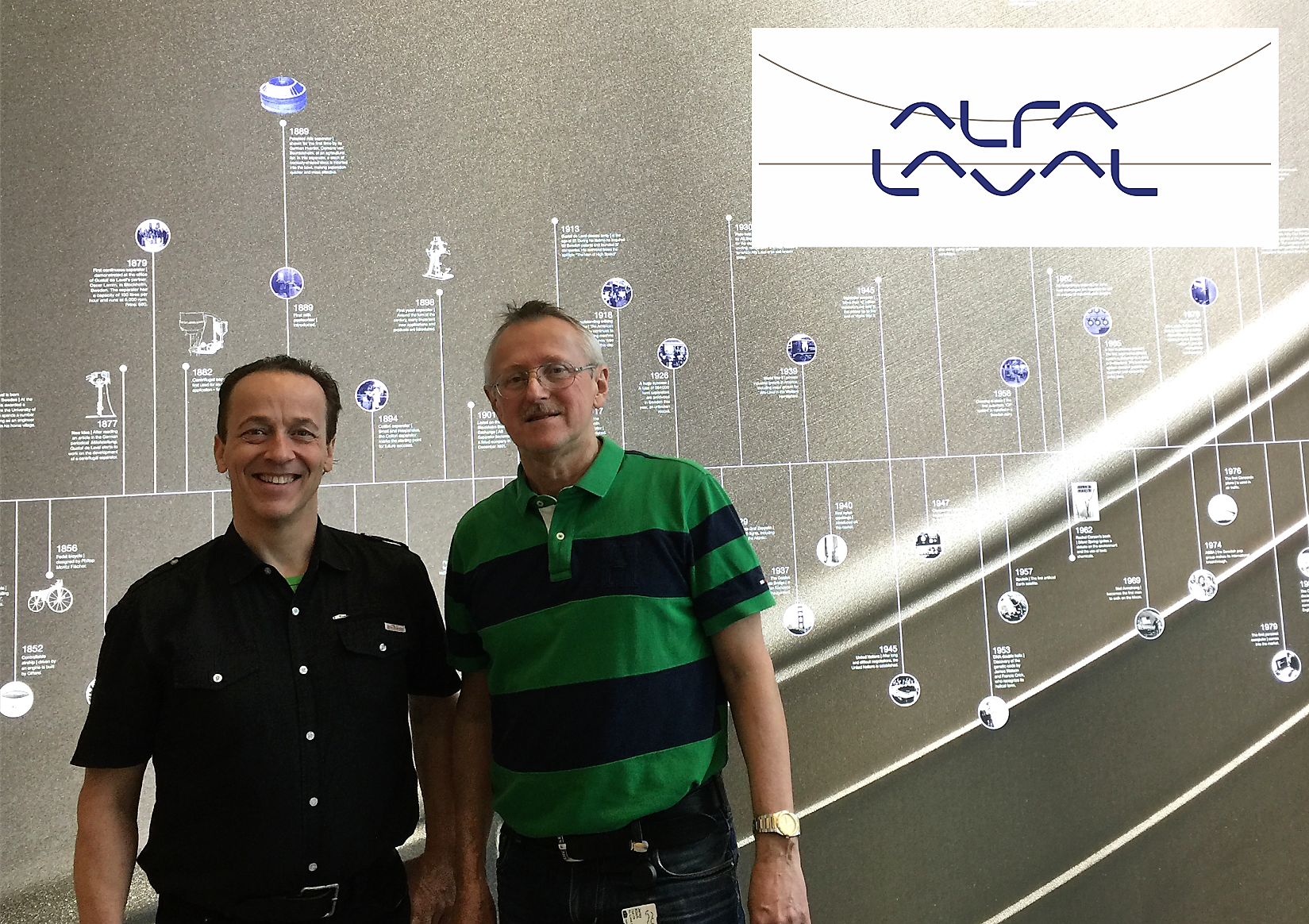
Alfa Laval Lund operates electric linear conveyor digitally
In 2015, Alfa Laval Lund bought their first electric linear conveyor from Conveyor 22. The task is to handle extremely light outflow cuttings within limited space. The conveyor needs to be controlled digitally via their system. The production runs continuously around the clock except for Christmas and Easter holidays. Jerzy Klich working with machine peripherals has given us this feedback:
– When I firstly contacted Conveyor 22, they responded quickly and explained what I wanted to know. They made me feel safe.
– I am satisfied to have chosen the right device now. Conveyor 22’s conveyor has not caused any stops since we put it into our production line two years ago. I can only recommend this electric conveyor. Everything about it is positive.
Jerzy Klich, Production Engineer, Alfa Laval Lund AB, 2017-03-29
Swep appreciates the compactness and freedom from maintenance
SWEP in Landskrona has bought several conveyors since 2015. In one of their big stamping tools, they integrated Black Line 141 and now we’ve got this feedback:
– Your conveyors are small and thereby easy to be built into a tool directly. The main advantages are reliability and compactness.
– After more than a year we have not had any problems. The tool works so well that it is seldom serviced and we are very satisfied.
Simon Jansson, Production Technician, SWEP International AB in Landskrona, 2017-03-17
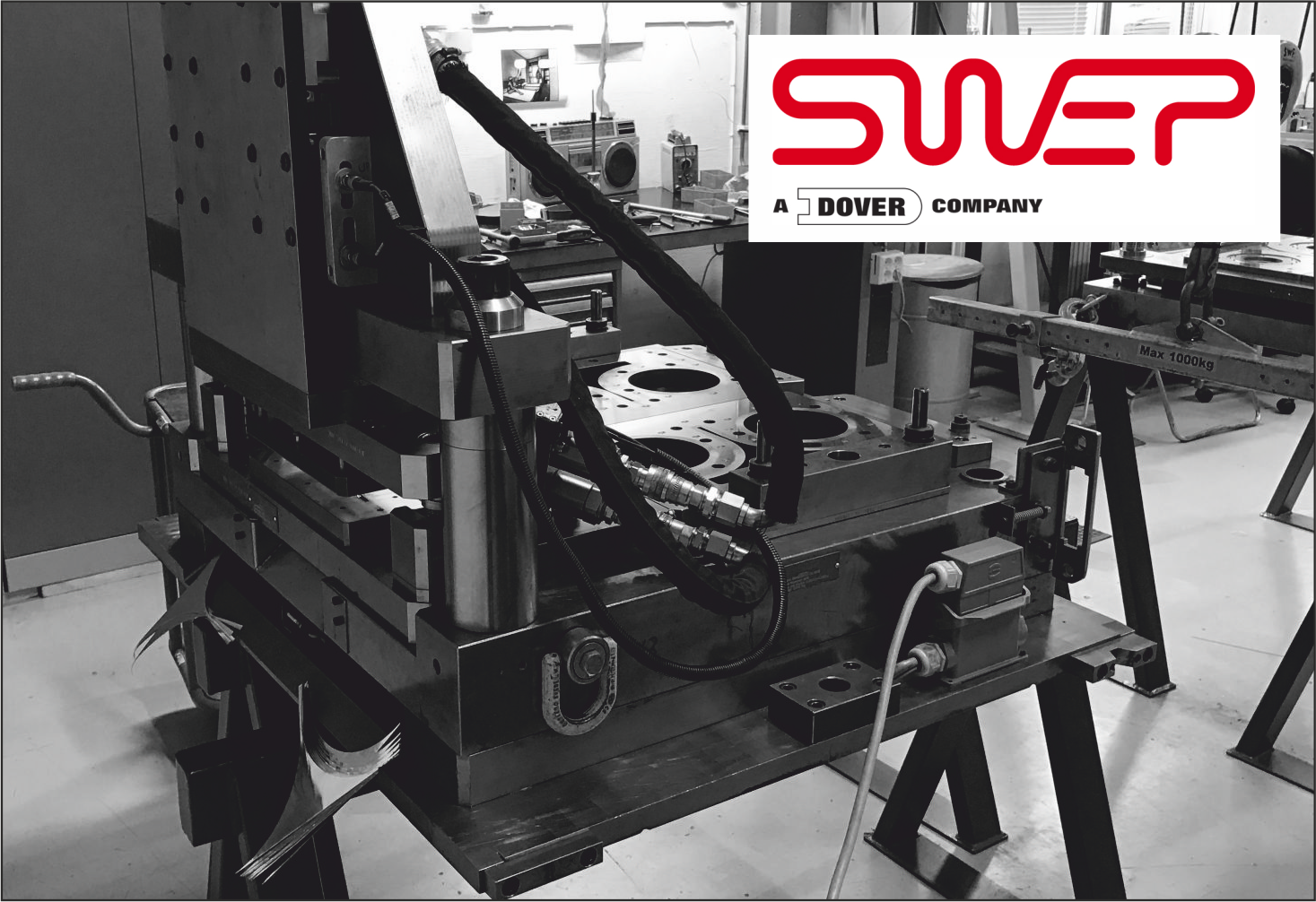
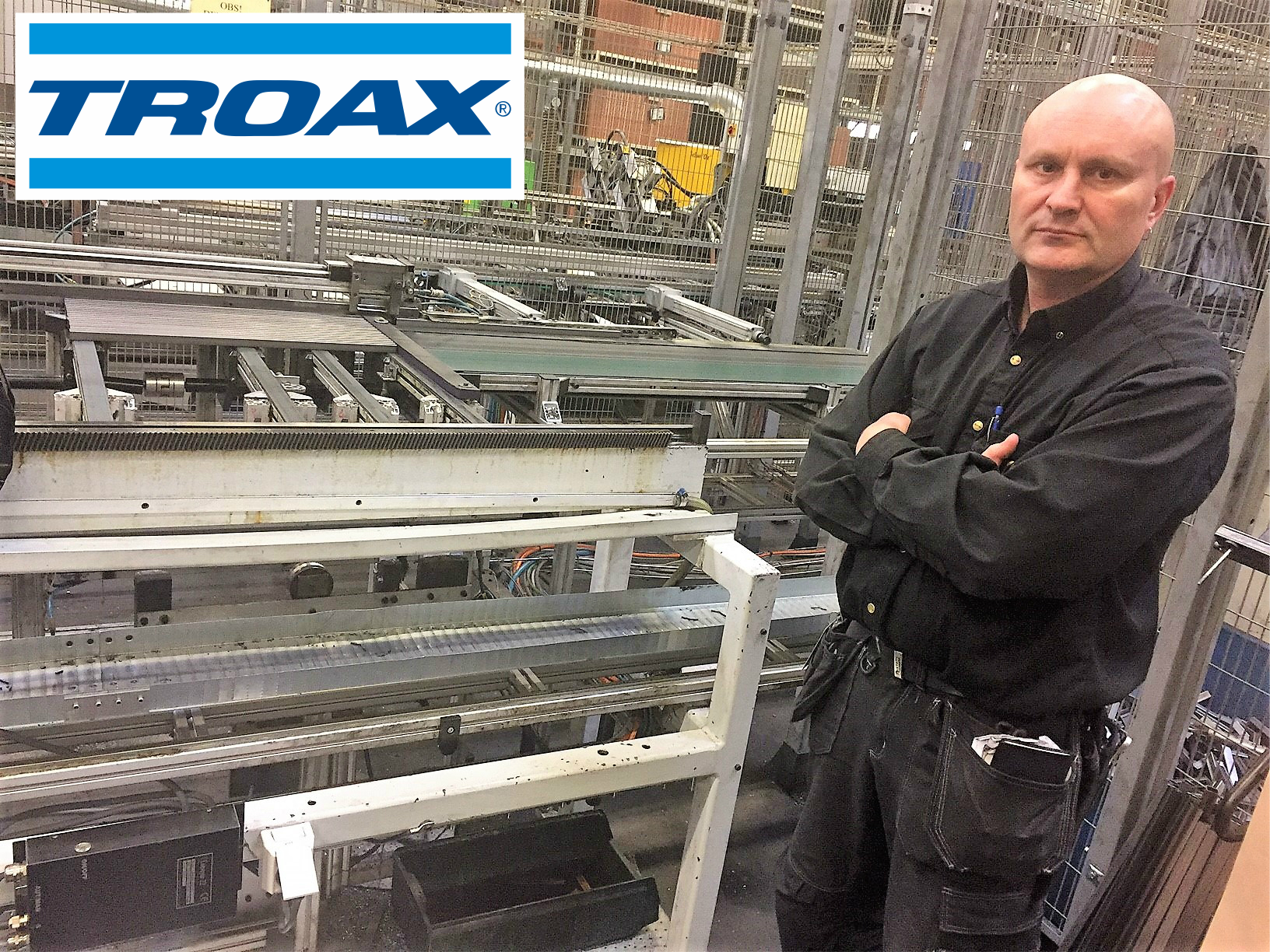
Troax replacing belt conveyor by electric linear conveyor
In February 2016, Troax bought their first Black Line 121 conveyor from Conveyor 22. On this output device, they equipped a 4.5 m long feeding tray = the longest tray we have delivered so far. The goal was to eliminate the maintenance from the existing solution of belt conveyor. Here is their experience on our electric conveyor’s solution after one year:
– When we use the belt conveyors, we are having problems that sometimes caused production downtime. The belts burst of the oil, they become slipper in a while, and they must be stretched after getting elongated. The scraps also tend to be trapped under the belts.
– With Conveyor 22’s conveyor, we have not had any problems whatsoever. It works really good!
Mika Lehto, Maintenance Technician, Troax AB i Hillerstorp, 2017-03-16
No place for output device – Quick Cassette fixes it!
At the beginning of 2017, EBP in Olofström bought two conveyors with insert fasteners “Quick Cassette” and feeding trays from Conveyor 22. Quick Cassette is a 85 mm high conveyor unit that can be pushed into the press tool. Feedback from the process engineer:
– Without this solution for our output problem, we had not been able to undertake this stamping project.
– The equipment has been working perfect since the first day. It is so quiet that you risk forgetting to turn it off when the working day is over.
Patrik Henriksson, Stamping Press Process Engineer in EBP i Olofström AB, 2017-02-25
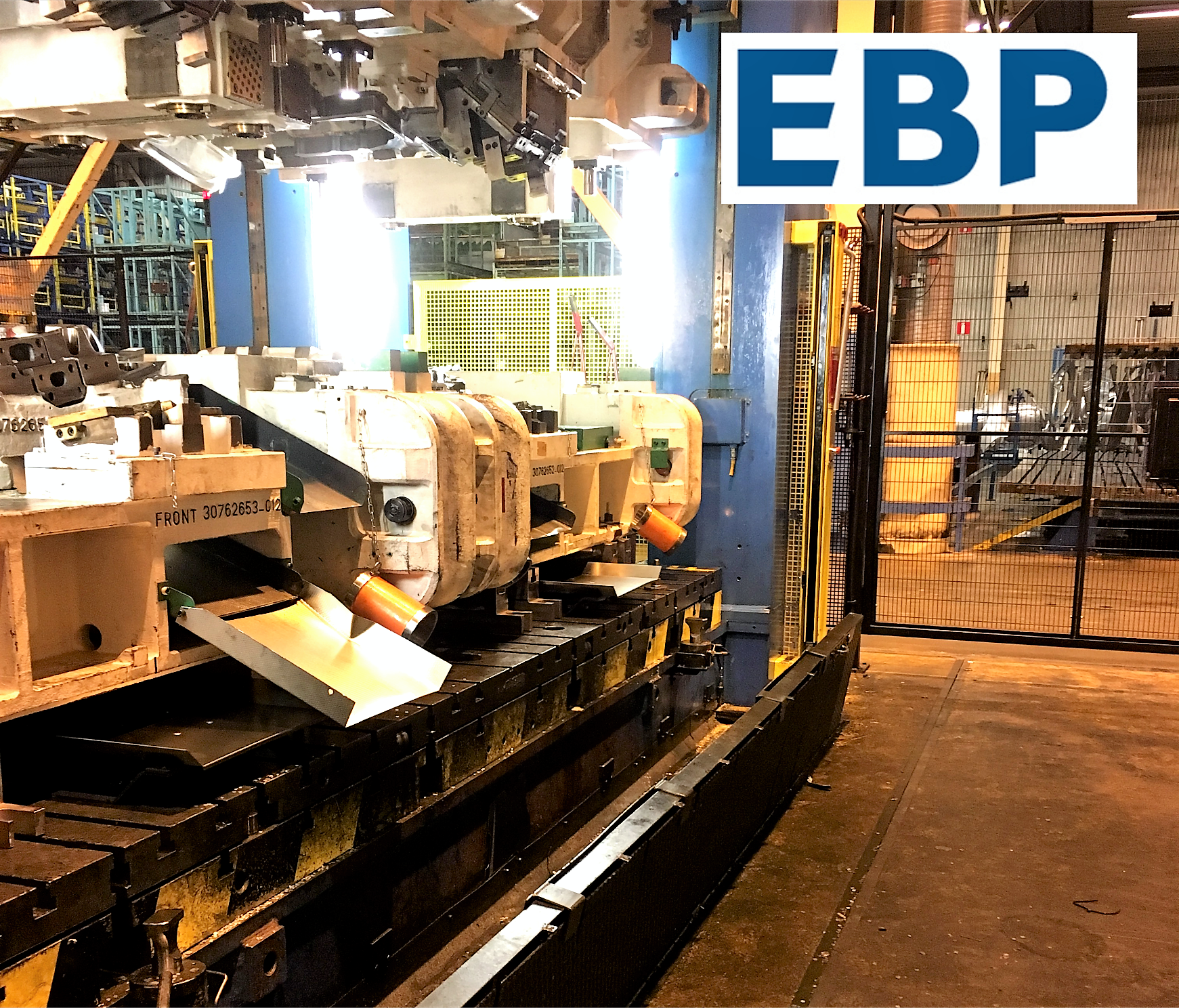
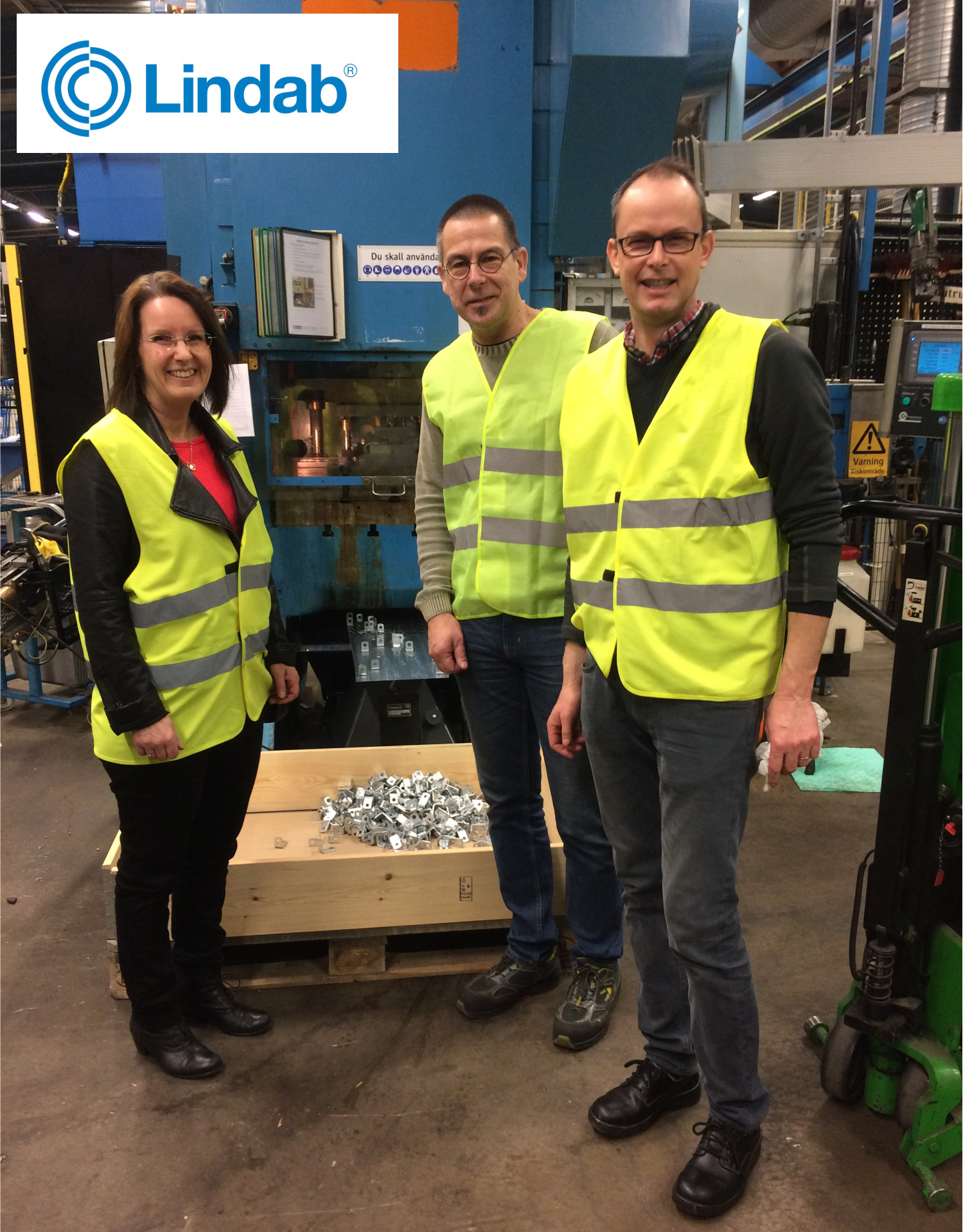
Picture from left to right: Anne-Maj Öström, Benny Nordh and Rickard Berg
Why build by ourselves when ” ready to go ” is available?
In the spring of 2015, Lindab Profile in Förslöv bought a conveyor from Conveyor 22 and built it into one of their stamping tools. The purchase was done through Rickard Berg, Bimex, one of Conveyor 22’s representatives.
Now for a different stamping press’ output, they equip with: one Black Line 141, Steady Stand 500 with the optional 3-wheel adapter and a tray support with sliding elements. The sorting feeding tray is developed by Lindab themselves.
– We are very pleased with the electric linear conveyor that we’ve been using for a while now. It’s really contrary to what we had before because it is so peaceful and quiet.
– When we bought this conveyor, I went through the product catalog and found Steady Stand. Immediately I thought: why do it by ourselves when there is already finished one available? Things can easily go wrong when you do it the first time as well as it is time consuming.
– The Steady Stand 500 we received today is stable and well-functioning.
Benny Nordh, Lindab Profil AB, 2016-12-07
Quick Bar brings the flexibility and simplicity
Industrias Metálicas Ruiz, a stamping company in north of Spain, bought Black Line 121, Quick bar and RC22 in February 2016. A feedback letter from the operation manager:
– Firstly, we were worried about the evacuation speed of the conveyor, but it proved that it is fast enough for our stamping press process.
– We are absolutely delighted with the flexibility and convenience from the equipment, it has really improved our automatic processes.
– The Quick Bar enables us to add several trays on the conveyor at the same time and we have saved several belt conveyors with their many wires and installations. The changing of stamping tools has now become really quick.
– The feeding trays also require less height than a regular belt conveyor.
Jesús Lobo, production manager in Industrias Metálicas Ruiz, 2016-06-08
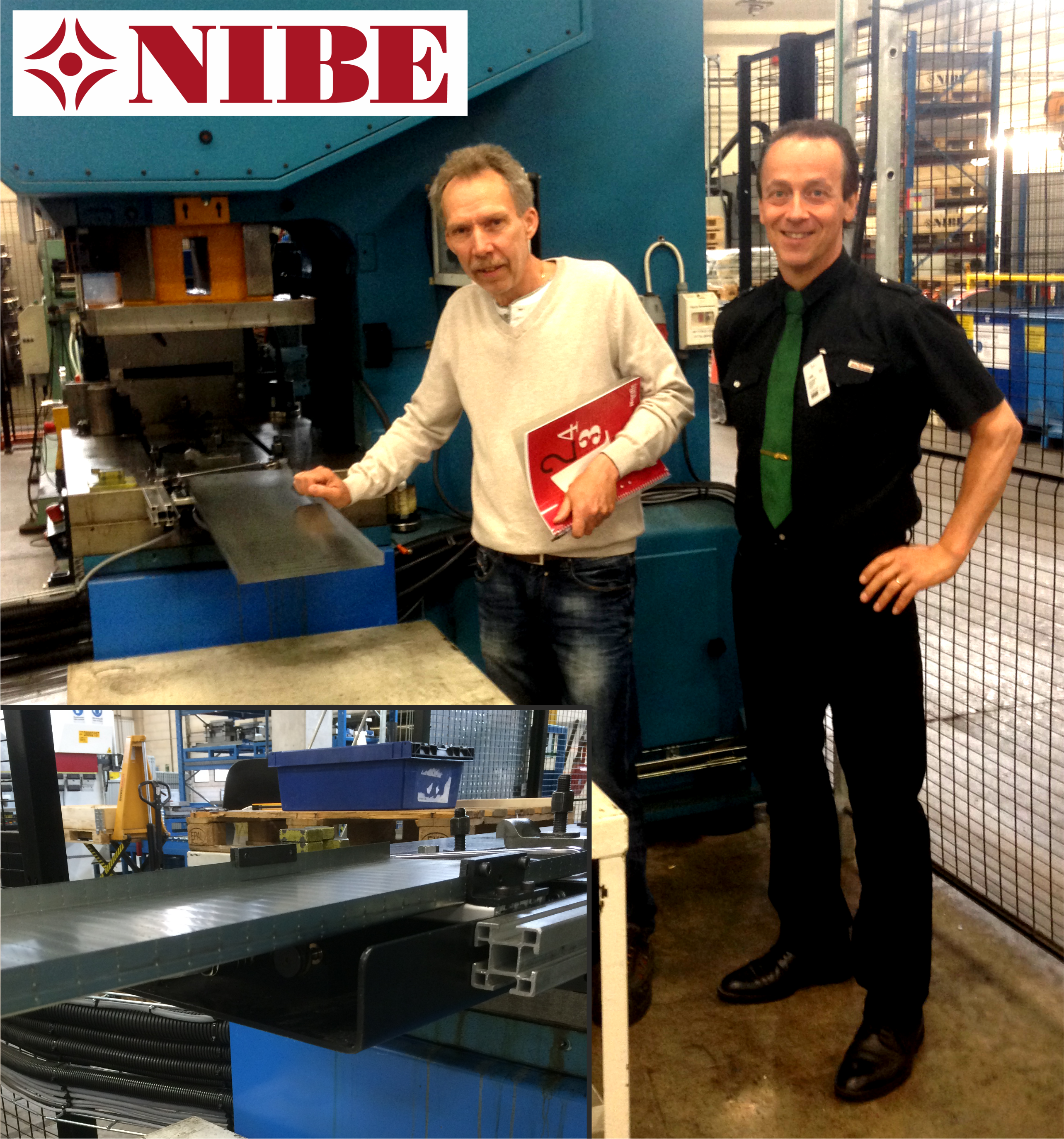
Better alternative for belt conveyor
Nibe in Markaryd have replaced belt conveyor with Black Line 141 and feeding tray RC22 in the production in early 2015.
– At first we were skeptical about the output speed, but now we are convinced by their excellent performance. We had belt conveyors before, but they were impossible to adjust in width according to all the stamping tools we have.
– It is so smooth and easy with feeding trays. We cut them in various sizes and adjust the width just as we want. It gives us completely different possibilities, and they are now used for everything.
– We are very satisfied!
Sven-Erik Hjelt, production technician in Nibe AB, 2016-05-30
SAPA Profiles recommend RC22
– We have used our conveyors for two years without any malfunctions.
– The longest feeding tray we have is over 4 meters. Ordinary plate did not work properly, but nowadays we use Conveyor 22’s metal RC22 and are very satisfied with the function.
Weine Stridh, SAPA Profiler in Vetlanda
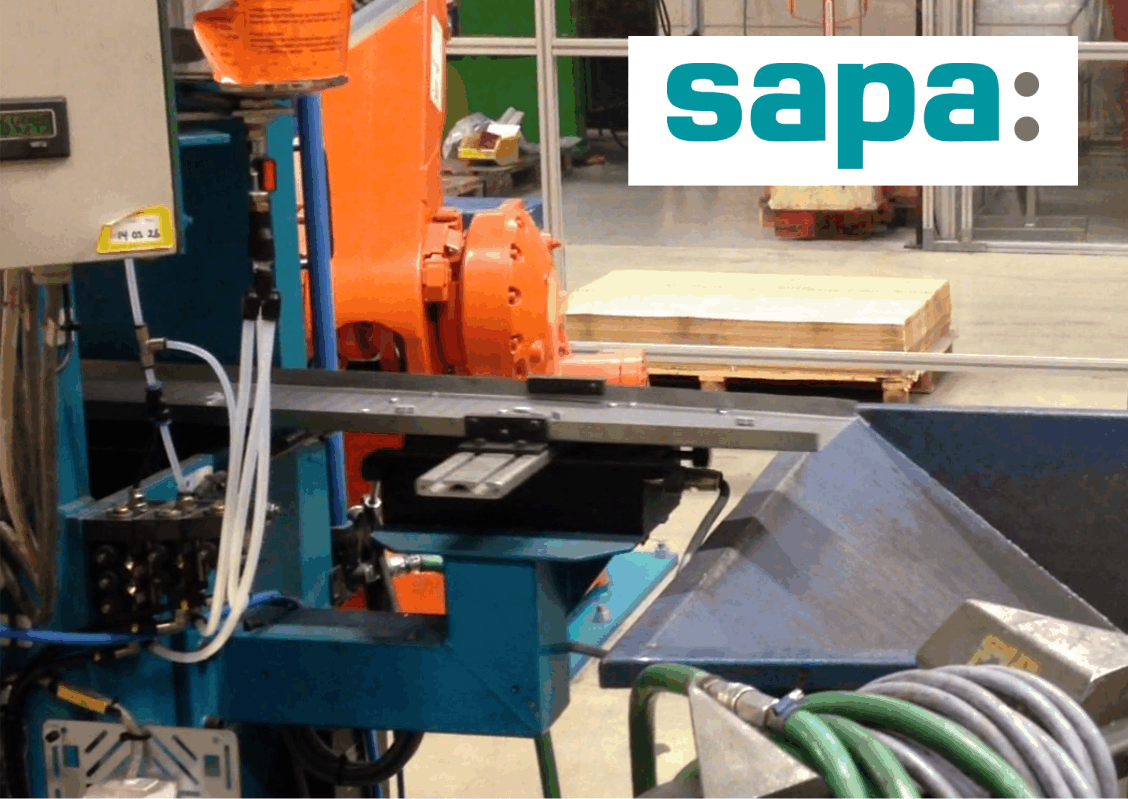
Ford Motor Company
ECS-121 Electric Conveyor has been delivered to the Ford Motor Company in the USA through our U.S. representative Wennberg International Traders LLC.
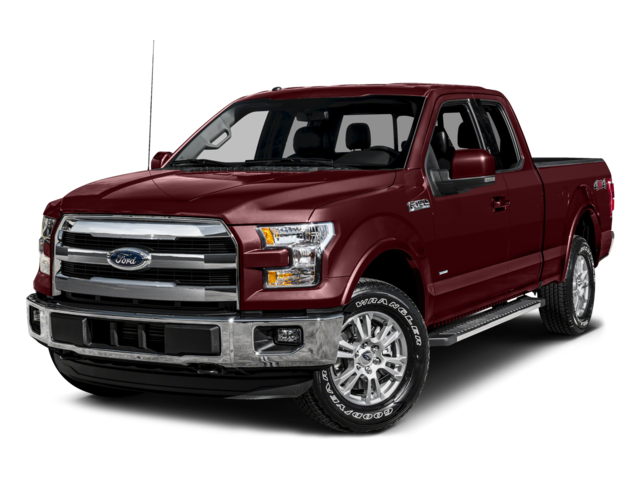